F/A-18 Hornet
Originally posted by @TyphoonCro on the old War Thunder forum
With many of topics for US 4th gens popping up, I thought I’d contribute as well with Hornet topic. This topic is work in progress and will be updated over time.
This topic will include the development and will showcase the variants of the Hornet family.
The Hornet at a Glance
Specifications of the F/A-18A/B/C/D:
Physical Characteristics:
- Crew - 1 (A/C) or 2 (B/D)
- Length - 56ft (17.07m)
- Wingspan (Without Missiles) - 37ft 6in (11.43m)
- Wingspan (With Missiles) - 40ft 5in (12.32m)
- Wing Area - 400sq ft (37.16sq m)
- Height to Fins - 15ft 3in (4.65m)
- Height to Canopy - 10ft 6in (3.20m)
- Empty weight - 22,000 - 23,000lbs (10,000kg) (approximately, depending on model)
- Max Takeoff Weight - 51,900lbs (23,541kg)
Powerplant:
- Engines:
- 2 x General Electric F404-GE-400 - Producing 10,600lbs (4,808kg) thrust dry, 16,016lbs (7,264kg) thrust afterburning (F/A-18A/B)
- 2 x General Electric F404-GE-402 - Producing 11,000lbs (4,990kg) thrust dry, 17,750lbs (8051kg) thrust afterburning (F/A-18C/D)
[/quote]
- Fuel:
- Internal Fuel - 10,860lbs (4,926kg)
- External Fuel - 3 x 2,210lbs (1,000kg) FPU-8/A drop tanks
Performance:
- Maximum Speed - 1,190mph (1,915kph) at 40,000ft (12,000m) - Mach 1.8
- Service Ceiling - 50,000ft (15,000m)
- Rate of Climb - 50,000ft/min (250m/s)
- Thrust/Weight - 0.935 (Afterburning with 50% internal fuel and suspended armament of 2 x AIM-9 + 4 x AIM-7)
Armament:
- Guns - 1 x M61A1 Vulcan 20mm Cannon (578 rounds)
- Hardpoints - 9 total: 2 × wingtips missile launch rail, 4 × under-wing, and 3 × under-fuselage
- Air-to-air Missiles:
- AIM-9 (1 x Pylon 1/9) (2 x Pylon 2/8) (2 x Pylon 3/7 - F/A-18A+/B+/C/D)
- AIM-7 (1 x Pylon 2/4/6/8) (1 x Pylon 3/7 - F/A-18A+/B+/C/D)
- AIM-120 (1 x Pylon 4/6 - F/A-18A+/B+/C/D) (2 x Pylon 2/3/7/8 - F/A-18A+/B+/C/D)
- AIM-132 (1x Pylon 2/3/7/8 - RAAF F/A-18A/B)
- IRIS-T (1 x Pylon 2/3/7/8 - SASF EF-18A/B)
- Air-to-surface Missiles:
- AGM-65 (1 x Pylon 2/3/7/8)
- AGM-84 (1 x Pylon 2/3/7/8)
- AGM-88 (1 x Pylon 2/3/7/8)
- AGM-158 (1 x Pylon 2/3/7/8)
- KEPD 350 (1 x Pylon 2/3/7/8)
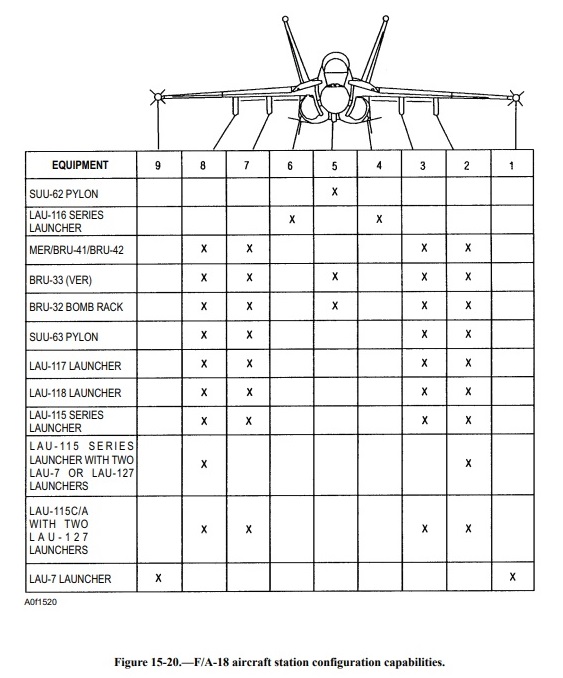
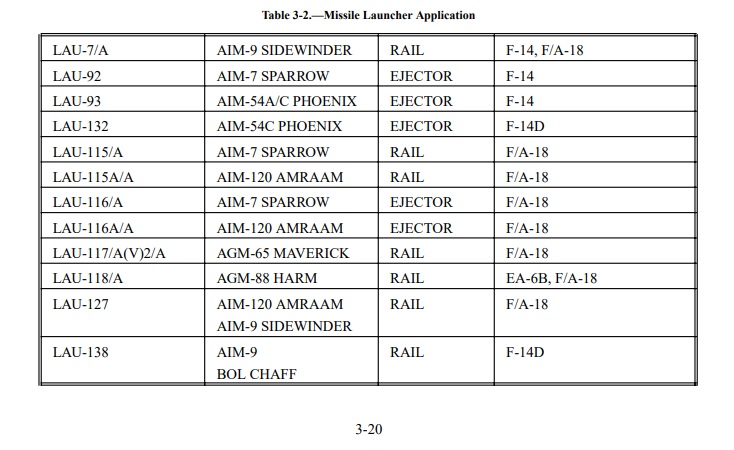
WIP
History:
Prelude to Cobra: The P530
Evolution of designs which culminate with the F/A-18 Hornet.
In 1978, the F/A-18 Hornet took to skies but the Hornets story started over a decade earlier with Northrop conducting studies for follow on designs to F-5. Over time, the design gradually evolved from slightly different F-5 to entirely new design and in 1967, the first of “Cobra” designs was born, the P530. The design was continuously improved and by the time USAF launched its Lightweight Fighter competition, Northrop was eager to enter. By 1972, the Northrop had refined design so much that the F-5 lineage was only barely visible.
Refined P530 design which would lay the foundations for the YF-17 Cobra.
The advanced technology features of the P530 were not confined merely to its shape and engines, but extended to electronics, armament and materials. Advanced radar enabled pilots for the first time to detect airborne targets at low as well as high altitudes. Nine external weapon station stations gave it a wide range of armament carriage in close support and air superiority mission roles. Finally, to lower cost and reduce weight, Northrop drew on its experience in graphite-epoxy composites, not only in the laboratory but also on F-5 reinforced structural components in actual usage, to apply the new materials to the P530.
Structurally, the tricycle-geared P530 was to be primarily of riveted aluminum alloy semimonocoque construction. Steel and titanium were used in the high temperature areas and for space-limited highly loaded components. Graphite-epoxy laminates and aluminum honeycomb were also used for certain doors and secondary structures.
Four bladder-type fuel tanks were located in the fuselage behind the cockpit, and single-point pressure refueling was provided. Polyurethane reticulated foam was used inside all tanks to prevent vapor explosions. The thin, dry wing was of multispar construction with thick, machined aluminum skins. It consisted of left-hand and right-hand panels attached to the fuselage with shear bolts. Aluminum honeycomb was applied extensively in panels, leading- and trailing-edge flaps and ailerons. The all-movable horizontal tail was an aluminum bonded assembly with honeycomb core. The twin vertical stabilizers were of thick aluminum skin with multiple spars and the rudders were aluminum-bonded assemblies with honeycomb cores.
As in the F-5, the twin turbojet engines were mounted side-by-side in the aft section of fuselage, except that the P530 engines were removed by lowering vertically without removing the horizontal tail or boattail. A three-point mounting arrangement permitted quick engine removal or installation. The engines were isolated from one another and from the forward airframe compartments by titanium firewalls. An integrated engine starter and accessory drive system was mounted on the airframe forward of the engines. By disconnecting the engine drive shaft from the power package, each engine can be removed without disturbing the electrical, hydraulic or gas turbine starter units.
The P530 was to be equipped with a single 20mm Gatling-type gun mounted in the upper forward fuselage. Alternate arrangements included two 30mm cannon or two 20mm cannon. In addition, four missile launcher rails were installed for IR missile carriage: one on each wingtip and two on wing pylons. A total of seven external pylon stations supplemented the two wingtip stations for a variety of ordnance or fuel stores.
The YF-17 is born
Among the first projects to be selected by the USAF for prototyping or “fly-before-buy” was a specialized lightweight fighter (LWF). The move was expected to promote creativity among the leading aircraft design teams as well as exploit technical advancements with flying hardware. A Request for Proposal was issued by the Air Force in the fall of 1971. It called for an aircraft highly specialized in the visual, clear weather, day-fighter role for air superiority over the battlefield with particular emphasis on light weight and low cost. The new fighter would have to sustain high rates of turn and increased maneuvering capabilities, while retaining the ability to accelerate readily. The LWF would incorporate no compromises which might detract from its ability to maneuver inside the “combat arena”.
No performance requirements were stated above Mach 1.6. Its role was to be confined to air superiority by limiting external stores capability and electronic equipment to a bare minimum. The prototype program was intended to evaluate advanced technology and design concepts, to determine aircraft capabilities, and to establish operational utility. Upon issuance of the RFP, it became readily evident that all of the P530 development work was applicable to the LWF. Following the refinement of the P530 design in accordance with the detailed RFP requirements, the company submitted its proposal to the Air Force in January 1972. The new design was designated “P600”. The P600 incorporated the GE 15J1A5 (later designated YJ101) with thrust increased to 14,400 pounds. In addition, the wing area was reduced to 350 sq/ft to improve supersonic performance.
At the conclusion of industry competition and proposal evaluation in April 1972, the Air Force announced Northrop and General Dynamics as winners, each to produce two flying prototypes. The Air Force designated the General Dynamics entry the YF-16 and the Northrop entry the YF-17. The Northrop team leaders were Walt Fellers, program manager; Tom Rooney, engineering manager; and Rex Thornhill, manufacturing manager. When the engineering development phase was completed, Roy Jackson became the program manager on through the flight test phase.
The YF-17 was a single-place, twin-engine fighter in the 20,000-pound weight class, featuring a high thrust-to-weight ration and low wing loading for maximum maneuverability. Advanced propulsion technology was closely integrated with advanced in aerodynamics, controls and structures. Features among these design innovations were hybrid wing with root leading-edge extension (LEX), differential area ruling, underwing inlet with wing slot for boundary layer bleed and active control features such as automatically controlled wing leading-edge and wing trailing-edge variable camber. In addition, 900 pounds of lightweight graphite composite materials were used in secondary structures and the cockpit was designed for high “G” maneuvering and optimal visibility.
YF-17 prototype No.1 rolled out of the Hawthorne plant in April 1974. It was trucked to Edwards Air Force base for flight test preparation. First flight took place on June 9, 1974, with Chief Test pilot Hank Chouteau in the cockpit. Following a 61-minute flight, Chouteau remarked, “When our designers said that in the YF-17 they were going to give the airplane back to the pilot, they meant it. It’s a fighter pilot’s fighter.” Two days later, the YF-17 flew supersonically in level flight without afterburner - “a first” for any US-built airplane. First flight of prototype No.2 was on August 21, 1974. By mid-January 1975, an accelerated seven-month flight test program was completed. A total of 288 flights, or 330 hours of flight test time, had been recorded. Prototype No.1 made 191 flights; Prototype No.2 made 97 test flights. The earlier aircraft was used for a majority of the test program elements, including flight controls development, flutter, airframe-propulsion compatibility, armament-propulsion compatibility, performance, and stability and control. The second aircraft was used for structural loads, stall/post-stall, and handling qualities during tracking. Both aircraft were employed simultaneously to evaluate operational factors and subsystems development-evaluation, and to asses reliability-maintainability.
The information obtained during the flight test program clearly established the high-performance and low-cost characteristics of the YF-17. The Air Force decided that the YF-16 would be better suited for its specific operational requirements, notably supplementing of its air-to-air fighter force and including considerations of its force structure mix and logistics commonality with the other aircraft already in service. The YF-17, designed to a concept of mission versatility and therefor providing a high degree of air-to-ground as well as air-to-air capability, went on to win the Navy air combat fighter competition where multi-mission suitability was a greater consideration. The YF-17 was selected by the Navy to be modified for carrier operations and was redesignated the F-18. The F-18 will replace the F-4 and A-7 in the US Navy and Marine Corps.
YF-18 Hornet
Picture from aviationarchives.blogspot.com
Rags to riches
Evolution from P530 to F/A-18 Hornet
Although the YF-17 lost the Air Force LWF competition to the General Dynamics’ YF-16, it would find another customer soon enough. The US Navy.
At the time the Navy was studying a new fighter, the Naval Air Combat Fighter (NACF) which would eventually replace the A-7. Since the F-14 was in some trouble at the time because of cost over-runs and the threatened shutdown of the production line by Grumman, which was being held to a contract that guaranteed they would lose money, the Navy wanted to make sure that its new NACF was capable of performing in the air-to-air arena.
Grumman’s financial problems were not the only thing that was causing the Navy to doubt the efficacy of building more Tomcats. The F-14s TF-30 engines, originally designed and built for the F-111, were the first afterburning turbofan engines. As such, they suffered many performance shortcomings which impacted the F-14s operational capabilities. In 1973, the Navy wasn’t just looking at an airplane to replace the A-7 and F-4, it was looking at a possible replacement for its brand-new F-14. The fighter branch of the Navy set forth requirements for a fixed-wing experimental fighter/attack (VFAX) aircraft. In June of 1974 requests for proposal were sent to General Dynamics, Northrop, McDonnell-Douglas and three others, who never got a chance to put pencil to paper because Congress rescinded the VFAX RFPs in August, directing the Navy to choose its VFAX from the lightweight fighter contenders.
General Dynamics and Northrop already had their VFAX contenders flying, McDonnell-Douglas did not, but they had the advantage of a great deal of experience in the design and construction of Naval aircraft. The Congressional mandate seemed to eliminate McDonnell-Douglas from the consideration, unless a collaboration, based on their expertise, combined with the existing LWF designs, could be forged. The YF-16 was chosen by USAF, based in part on its longer range and use of the F100 engine, which was in production for the F-15. It was not McDonnell-Douglas’ choice. They favored the YF-17 and approached Northrop to act as a partner in the development of the YF-17. Northrop agreed to McDonnell-Douglas being prime contractor, probably because the P530 had traveled a long and troubled road, rejected by a host of foreign users and the USAF. The VFAX, now NACF, seemed like the last chance, and having a partner like McDonnell-Douglas must have seemed like a great way to finally sell the design.
F/A-18 Hornet and F-15 Eagle in flight
The US Navy announced its choice for NACF as the McDonnell-Douglas Northrop design on 2 May 1975. Although visually similar, the F-18 Hornet, as the new design was christened, was not a modified version of the YF-17. It was quite similar in size and shape, but the task of navalising and multi-tasking of what had been designed as a land-based single-purpose technology demonstrator required a new design. Congress has dictated that the winning LWF design be developed as a multi-service airplane. General Dynamics collaborated with LTV to develop a carrier-based version of the F-16 and they expected it to be bought by the Navy. The wording of the Congressional mandate left room for argument that the Navy might choose from either of the LWF designs and, after examination of both, McDonnell-Douglas determined that the YF-17 was a better design for the NACF submission. After a lot of political in-fighting, the McDonnell-Douglas/Northrop partnership won their argument.
It was first thought that the Hornet would be built in two versions: F-18, optimized for air-to-air combat and A-18, for the attack mission. It very quickly became apparent, however, that the Hornet would have the capability to perform both tasks, so it was redesignated the F/A-18. The F/A-18 differed from the YF-17 in a number of ways. One of the most basic changes needed was the overall strengthening of the airframe to withstand the rigors of carrier operations. Radical redesign of the landing gear was necessary and this is perhaps the most noticeable of the many changes made in the basic YF-17 design. Other changes made included lengthening and widening of the fuselage to increase internal fuel capacity from 5,500 pounds to 10,800 pounds, an increase in wing area from 350 sq/ft to 400 sq/ft, a span reduction and chape change to the horizontal stabilators to accommodate storage and enlarging the nosecone to accommodate a multimode radar.
The F/A-18A made its first flight on 18 November 1978, with McDonnel-Douglas chief test pilot Jack Krings at the controls. This flight was made from the McDonnell Aircraft facility at Lambert Field, St. Louis. The number one Hornet (BuNo 160775) was the first of nine single-seat full scale development aircraft, and two two-seat TF-18s to take part in the test program, which was conducted at the Naval Air Test Center, NAS Patuxent River, Maryland.
The test program, which lasted nearly four years, was one of the most extensive and trouble-plagued programs ever endured by the Navy. Much of the trouble was caused by the double digit inflation of the late 1970s, which caused the inevitable cost over-runs and periodic Congressional outcries for cancellation of the entire F/A-18 program. The Hornet design overcame all the negatives though and the first operational Hornet squadron, VFA-125, was commissioned at NAS Lemoore, California on 13 November 1980, as the fleet readiness squadron or RAG.
Continued in next chapter (F/A-18 & F/A-18B) below.
F/A-18A & F/A-18B Hornet
- The first variant to see service with USN and USMC. The 18A was a single seater variant while the 18B was a two seater fighter.
Hornet in detail
The heart of the F/A-18’s weapons system is the Hughes AN/APG-65 multimode pulse Doppler radar. The radar is operated in several modes, including Boresight, Vertical Acquisition and Head Up Display during air combat maneuvering (ACM). These modes feature automatic acquisition of maneuvering targets at ranges of 500 feet to five nautical miles. Another ACM mode is the Gun Director Mode, which is a special short range track mode. The radar’s high pulse repetition frequency (PRF) makes it very effective in long range tracking of nose aspect targets, giving velocity and azimuth information. Range-While-Search uses high and medium PRF to detect all-aspect targets, and Track-While-Scan maintains ten target track files, displaying eight. When the Advanced Medium Range Air to Air Missile (AMRAAM) missile becomes operational, the F/A-18 will be able to simultaneously attack as many targets as it has missiles to shoot. The Raid Assessment feature of the radar allows the pilot to expand the region centered on a single tracked target, giving increased resolution in the target vicinity, which permits radar separation of closely spaced targets.
In the air-to-ground attack role, the APG-65 has a number of modes including: long range surface mapping which enhances target location and identification, navigation and weapons delivery. High resolution mapping, combined with additional modes of the radar, give the pilot the ability to detect and track fixed, moving and sea surface targets, as well as the ability to cue other sensors such as the Forward Looking Infrared (FLIR). A terrain avoidance mode is available for low-level night or bad weather penetration missions. A precision velocity update feature improves navigation accuracy by automatically updating the inertial navigation platform. It also serves as the doppler input to weapons delivery computation. A sea surface search mode suppresses sea clutter by sampling the sea state and setting a threshold above that of sea clutter. Two-channel monopulse angle tracking and coherent frequency agility allows accurate tracking of ground fixed or moving targets, and air-to-surface ranging is provided by the radar through use of split-gate range tracking at large depression angles, or elevation monopulse tracking at small depression angles. Designation of the target provides automatic acquisition in this mode, and designation can also be provided by the laser spot tracker or by FLIR.
These capabilities were provided by the fully software programmable signal processor, which performed 7.2 million operations per second. The APG-65 was extremely reliable, with it being qualified for the 106 hours mean time between failure (MTBF) standards set by military test procedures. Shop replaceable assemblies, no scheduled maintenance requirements, and the fact that no special maintenance tools were needed, made maintenance faster and easier for military technicians, which translated to a higher in-service rate for operational Hornet squadrons.
Although it was capable of carrying up to 17,000 pounds of ordnance, the F/A-18 was designed with only one internal weapon, a six-barrel 20 millimeter (mm) Vulcan cannon. This weapon was finally included in the Hornet after a lengthy battle between the combat aviators who suffered through the Vietnam War in F-4s without an internal gun and the engineers who were concerned about the 5,000 pounds of weight the gun, ammunition, and gas required to carry it added to the basic airplane. The aviators finally prevailed in having the gun added and in having it placed where it would be most accurate and reliable - on the centerline of the airplane, in the nose, right next to the radar. In having the gun added, the aviators created some tough problems for the designers. The 20mm Vulcan was capable of firing up to 6,000 rounds per minute. This rate of fire caused vibration and generated a lot of heat, gas, and smoke, all of which was harmful to the reliable operation of sophisticated radar. The radar compartment could be sealed to keep out gas and smoke, and the cooling could be augmented. However, dealing with the vibration was tougher. This task required identifying the gun vibration frequencies and building baffles to dampen out their effects on the radar.
All combat functions for air-to-air and air-to-ground attack could be operated from the controls on the throttles and stick grip (Hands-On-Throttle-And-Stick or HOTAS has since become another standard for modern fighter design). Like other fighters of its generation, the primary information display was the Head-Up-Display (HUD) on the gunsight glass. The HUD displayed airspeed, altitude, vertical speed, AOA, heading, Mach number, Gs, and a variety of weapons delivery information. The older, round barometric instruments, which were located in a bottom corner of the panel, were relegated to a backup role. Aircraft systems were monitored with the information displayed on CRTs and managed with the 20 push buttons that surrounded each of those CRTs. The benefits of having all the necessary information within the pilot’s immediate field of view were reduced fatigue and a reduced susceptibility to vertigo. The preceding generations of fighter aircraft had dozens of controls and gages on the cockpit consoles, which often required a pilot to look down, left, right, or even slightly to the rear in order to use them. This constant movement was a sure-fire recipe for vertigo when outside visual cues were not sharply defined.
As far as weaponry is concerned, Hornet capability is impressive and the aircraft is compatible with a vast array of ordnance, encompassing air-to-air missiles, air-to-surface missiles, conventional “iron” bombs and “smart” weapons. The primary weapons, when employed in the air-to-air role, are the AIM-7 Sparrow and the AIM-9 Sidewinder. Missile configurations may vary, the F/A-18 being able to operate with maximum of six AIM-9s and two AIM-7s or, alternatively, four AIM-7s and two AIM-9s. The Hornet is particularly well-equipped for target detection, and if it can be said to have an “Achilles heel” in aerial combat, this probably relates to the Sparrow missile. The third weapon which may be employed in aerial combat is the Vulcan M61A1 20-mm cannon which also has air-to-ground applications. Total ammunition capacity is 570 rounds, with maximum rate of fire around 100 rounds per second.
In air-to-ground mode, the weapon options are truly bewildering, especially if target detection devices are fitted. With regard to payload potential, the F/A-18A may operate with up to 17,000lbs (7,711kgs) of ordnance, which typically includes a pair of wingtip mounted AIM-9 Sidewinders for self-defense. Such a payload would however rarely be carried and in more normal situations, auxiliary fuel tanks would almost certainly be fitted, the centerline and inner wing stations being able to pump in fuel. Offensive weaponry is then restricted to the two outer underwing hardpoints but the F/A-18 could still do a fair bit of damage, typical weapon configurations including four Mk.83 1,000lb (454kg) or two Mk.84 2,000lb (907kg) bombs or four “Rockeye” cluster bomb units (CBUs) or, for a real heavyweight punch, two B57 or B61 tactical nuclear weapons.
As far as conventional ordnance is concerned, low-drag “slicks” and high-drag Snakeye bombs may be employed while laser-guided Paveway versions of the Mk.82, Mk.83 and Mk.84 can be used against pin-point targets. Other “smart” weapons with which F/A-18 is compatible include electro-optically guided devices such as the AGM-62 Walleye glide bomb and the AGM-65 Maverick air-to-surface missile. Both of these weapons feature a small television camera in the nose, which generates pictures which are presented on one of the cockpit displays. All the pilot then has to do is locate the target and lock on it, as steering instructions are relayed automatically by data link. Later version of Maverick incorporate infra-red or laser seekers, which are particularly effective at night or in conditions with poor visibility.
Possessing greater range, the AGM-84 Harpoon is primarily intended for use against shipping and utilizes active radar homing during the terminal stages of flight. A “fire and forget” weapon, Harpoon is highly resistant to countermeasures, although its greatest disadvantage is that its radar cannot discriminate between “high” and “low” value targets.
The engine used in the F/A-18 Hornet was General Electric F404, formerly known as the YJ-101 during the YF-17 Cobra testing. General Electric was particularly anxious to make this engine successful since Pratt & Whitney was already making engines for the F-14, F-15 and F-16. The F404 engines installed in the Hornet had close tot the same thrust as the General Electric J79 engines, which powered the F-4. Thrust commonality was where the similarity ended between the two engines. The F404 was half the weight, was one-third shorter, had 40 percent fewer parts, was four times more reliable, could be installed on either side of the Hornet, was smokeless, and had the same responsiveness as the J79 although through greater range of operation. The Hornet demonstrated better than a 90 degree angle of attack (AOA) with a 45 degree angle of side slip. The J79 was one of the great fighter engines of the jet age, but the newer F404 showed how much the state of the art had advanced. The performance of the engines provided a significant improvement over the F-4 and A-7, which the F/A-18 would replace. On-board fire extinguishers allowed the pilot to put out fires quickly.
The fuel system had two self sealing, independent feed tanks and self-sealing fuel lines which were contained within the tanks. The wing tanks had foam, and all fuselage voids had foam. No fuel tanks were located between or around the engines, and no electrical power was needed to transfer or feed fuel to the engines.
Migration of Hornets
The first international user of the F/A-18 was the Canada and its fleet of 138 Hornets is the largest outside the United States. The CF-18 operated out of Canadian Forces Base in Cold Lake, Alberta, and Canadian Forces Base in Bagotville. The first CF-18B, a two seat model of the Hornet, was delivered on 26 October to the Canadian Forces 410 Squadron at Cold Lake. This squadron accumulated more than 100,000 flight hours and trained almost 60 pilots in CF-18s. Phase I of the Canadian Hornet Modernization Program was completed in August 2006. This program upgraded the Canadian Hornet fleet’s avionics, radio and weapon capabilities. Phase II of the CF-18 modernization program added a data link system, a helmet-mounted sight system, new color cockpit displays and a new chaff-and-flare-dispensing electronic warfare system to 79 CF-18 Hornets. Unlike other variants of Hornets, the CF-18 is the only one with the spotlight on the left side of the nose for air defense visual identification at night.
Australia is another user of Hornet and first Hornet was delivered to the Royal Australian Air Force (RAAF) on 29 October 1984. “F-18A” was the original company designation; designations of “AF-18A” & “ATF-18A” have also been applied. Subsequent to delivery of the first two MDD-built F-18s, Aero-Space Technologies of Australia (ASTA) assembled the Aussie Hornets from kits produced by MDD. Some parts were eventually manufactured in Australia. The most notable differences between an Australian (A)F-18A/B and its American counterpart were the lack of a catapult attachment, replacement of the carrier tail hook for a lighter arresting hook, and replacement of the automatic carrier landing system with an Instrument Landing System. Australian Hornets have been involved in a number of major upgrade programs. This program, called Hornet Upgrade (HUG), has had few evolutions over the years. The first evolution was completed in 2002. Hornets were upgraded to C/D model avionics and included replacement of the APG-65 radar with the APG-73. The second upgrade program (HUG 2.2) updated the fleet’s avionics to beyond E model Hornet capability.
Spain bought 72 Hornets (60 single-seat EF-18A, and 12 two-seat EF-18Bs). The Spanish Air Force designation was C-15 for the A model and CE-15 for the B model. Initial deliveries began in July, 1986. Spanish Hornets performed the all-weather interceptor role and were initially ordered with AIM-7 Sparrows and AIM-9 Sidewinders. The Spanish Hornets were subsequently upgraded for the AIM-120. The air-to-ground mission is flown using a variety of Spanish armament.
F/A-18C & F/A-18D Hornet
- Upgraded variants with more powerful engines and expanded weapon capabilities which included the AIM-120 AMRAAM.
Giving Hornet even more stinging power
The advanced F/A-18C made its first flight on 3 September 1986 from Lambert Field in St. Louis, Missouri with MDD test pilot Glen Larson at the controls. The F/A-18C was the culmination of an improvement program aimed at making significant improvements to the basic F/A-18A. The prototype was delivered to the NAS Patuxent River for testing, and the first production F/A-18C was delivered just a year later. Although the only external changes were the addition of several new antennas, the capabilities of the Hornet were upgraded by giving the aircraft the capability of launching the AIM-120 AMRAAM and the IR imaging AGM-65 Maverick. The F/A-18C was also equipped with the AKY-14 (XN-6) Mission Computer, which had an increased memory (twice as much as its predecessor) and a faster processor.
In 1990, Hughes Aircraft began work on an upgrade of the APG-65 radar under a $223 million full-scale development contract. The new radar, designated APG-73, had three times the speed and memory of the APG-65 and would be installed in new production Hornets beginning in 1994. Additionally, the new radar could be retrofitted on all F/A-18C/D aircraft. The Hughes APG-73 radar had the ability to detect airborne targets at more than 100 miles, distinguish low-flying or slow-moving targets “on the deck”, pinpoint ships at sea, map the contours of the ground, and track ground targets. F/A-18Cs had synthetic aperture ground mapping radar with a Doppler beam sharpening mode that generated ground maps. The ground mapping mode capability gave crews the capability to locate and attack targets in adverse weather and poor visibility or to precisely update the aircraft’s location relative to targets during the approach.
Forty eight F/A-18D, two-seat Hornets were configured as the F/A-18D(RC) reconnaissance version. With this version, the M61A1 cannon was replaced by a pallet-mounted electro-optical suite comprised of a blister-mounted IR line scan and two roll-stabilized sensor units, which recorded on video tape. The pallet-mounted gun and external gun compartment doors were removed and replaced by the camera system and bulged camera compartment doors that contained the camera windows. A fairing over the gun port completed the conversion.
From 1989 onward, production Hornets were delivered with night attack capability provided by GEC Avionics night vision goggles (NVGs), which worked by amplifying the moonlight, starlight, or reflected light from ground sources. The F/A-18C Night Attack Hornet had a pod-mounted AN/AAR-50 thermal imaging navigation set (TINS) mounted on a fuselage station, a Loral AN/AAS-38 Nite Hawk FLIR targeting pod, and GEC Cat’s Eyes pilot’s night vision goggles. The Hughes AAR-50 FLIR, contained in the (TINS) pod, was linked to a Kaiser HUD. The NVG compatible cockpit displays provided subdued instrument lighting necessary to maintain the effectiveness of the NVG goggles. Information from multifunction displays and a color digital moving map display were stored on a laser disk to provide intelligence information. The F/A-18C and two-seat F/A-18D Hornets were equipped with a flight incident recorder and monitoring set (FIRAMS) commonly known as “the black box”. The FIRAMS was linked with an integrated fuel and engine indicator and data storage set for recording maintenance and flight incidents data. A signal data processor interfaced with the fuel system to provide overall system control and enhanced BIT capability and automatic center-of-gravity adjustment as fuel was consumed.
Beginning in 1988, production Hornets were delivered with a “LEX Fence” installed on the top of each wing LEX. The LEX Fence was a 32 inch long by 8 inch high piece of metal, which reduced fatigue on the vertical tails and increased the service life of the F/A-18. The LEX Fences were retrofitted to all Hornets that remained in service. The LEX Fence was developed after cracks were found in the vertical fins of F/A-18A/B aircraft. The cracks were caused by the LEX vortices created by high AOA maneuvers. Since the Hornet lived at high AOA in combat, a fix was critical to its continued service and an 8 month test program was conducted to find proper shape, size, and placement of the LEX Fences.
In 1992, F/A-18C/Ds on the production line were retrofitted with the more powerful General Electric F404-GE-402 engines, which had 20 percent more thrust than the original F404-GE-400 engines used on earlier Hornets. The first production Hornets with the new engines were export models for Kuwait which were delivered during early 1992. Other avionics installed in the F/A-18C included a Collins AN/ARN-118 TACAN, AN/ARC-182 UHF/VHF comm and DF-301E UHF/DF, Magnavox AN/ALR-50 and Litton AN/ALR-67 Radar Warning Receivers, GEC Ferranti Type 117 laser designator, Goodyear AN/ALE-39 Chaff Dispenser, Sanders AN/ALQ-126B ECM, Harris AN/ASW-25 radio data link, Baton AN/ARA-63 receiver-decoder, GEC Ferranti FID 2035 horizontal situation indicator (HSI), Bendix/King HSI, J.E.T. ID-179 I/A flight director indicator, and the Litton AN/ASN-130A inertial navigation system plus global positioning system. Displays are on Kaiser multifunction CRTs, GEC Ferranti-Bendix/King CRT, Kaiser AN/AVQ-28 HUD, and ITT/Westinghouse AN/ALQ-165 airborne self protection jammer (ASPJ). However, the budgetary constraints forced the cancellation of the ASPJ program, which left F-14D and F/A-18C/D without internal electronic countermeasures (ECM) protection. Subsequent combat experience forced the military to authorize additional funding for the ASPJ pending development of a more robust system. 123 ASPJ were acquired in the end.
F/A-18C/D exports
The Kuwait Air Force ordered 40 C and D models in 1988. Although the Gulf War delayed delivery, the first Kuwaiti Hornets were delivered in January 1992. Kuwaiti Hornets were flown by Numbers 9 and 25 Squadrons and were based at Amed al Jaber AB. Kuwait’s Hornets were designated KAF-18C/D.
The 26 May 1997 delivery of four two-seat model Hornets to Malaysia market the first completion of an order placed by the Royal Malaysian Air Force (RMAF) in June 1993. The first four aircraft were delivered on schedule to Malaysia. Eight U.S. Navy and USMC pilots manned the controls as the aircraft made their way to Malaysia. The four Hornets were accompanied by a KC-10 tanker that provided air-to-air refueling. En route Malaysia, the crew made stopovers in Hawaii and Guam. The eight Hornets fulfilled strike and interdiction missions as part of the RMAF modernization program. Initially, the aircraft were used to train RMAF pilots. Boeing provided the logistical package that supported aircraft operations at the RMAF base at Butterworth. The RMAF Hornets were equipped with the upgraded Hughes APG-73 radar and two General Electric F404-GE-402 enhanced performance engines (EPE). Malaysia was the first nation in Southeast Asia to purchase and receive the F/A-18.
Finland acquired F-18s after an extensive multi-country evaluation that included the F-16, Mirage 2000, SAAB Gripen, and MiG-29 and 31 fighters. Letters of offer and acceptance were issued on 5 June 1992. Finland used F-18C/D Hornets with specific Finnish mid-life update. The Finnish Hornets lacked certain avionics and target acquisition and weapons control features, which limited their ground attack capability. The 7 F/A-18Ds were built by MDD, but Finland-based Patria assembled the 57 single-seated F-18C model units.
Switzerland’s acquisition of the Hornet was similarly tortured. The Kommando der Flieger began looking for a replacement for their Mirage III and F-5 fighters in the mid-80s. Initial competitors included the F-16 and Mirage 2000. Later in, the Israel Aircraft Industries (IAI) Lavi, Northrop F-20, and SAAB Gripen were also competitors. The Kommando der Flieger selected the Hornet in October 1988 with 34 F/A-18s ordered however it wouldn’t be until 1996 that first Swiss Hornet would be rolled out of the factory.
Reference
Sources
-
Northrop - An aeronautical history - Authored by Fred Anderson - Published by Northrop Corporation
-
F/A-18 Hornet in action - Aircraft Number 136 - Squadron/Signal publications - Lou Drendel
-
F/A-18 Hornet in action - Aircraft Number 214 - Squadron/Signal publications - Lou Drendel (more or less the same as previous source but newer)
-
Osprey Combat Aircraft Series - F/A-18 Hornet - Osprey Publishing - Lindsay Peacock
-
F/A-18 Strike Fighter brochure - McDonnell Douglas Corporation
-
Uncovering Boeing F/A-18A/B/C/D Hornet - Danny Coremans & Nico Deboeck - DACO Publications (big thank you to @spacenavy90 for providing this source)
more to be added
Disclaimer
I do not have much experience on either forum and as such I cannot make any guarantees on how often or how accurately this will be updated, however I am open to constructive criticism and advice as this is a topic that greatly interests me.
Please be kind.
Credit again to @TyphoonCro for the original post.