I’m starting this thread to lay out the information that I have on Tungsten cored projectiles. I had done a thread similar to this on the old forums, a long time ago. But, I’ve also found and learned a lot more since then. I’ve also learned how to properly model the projectiles in programs like Fusion 360, which has helped a lot… Especially for those projectiles where there is no information about the mass of the core.
This post is still kind of a work in progress, as I may add some images and documents to it, as I have time.
I’ll start with APCR and HVAP.
In general, I refer to the classic arrowhead-shaped composite rigid shells, as APCR.
They look like this.
Click to see Arrowhead type APCR shell diagrams
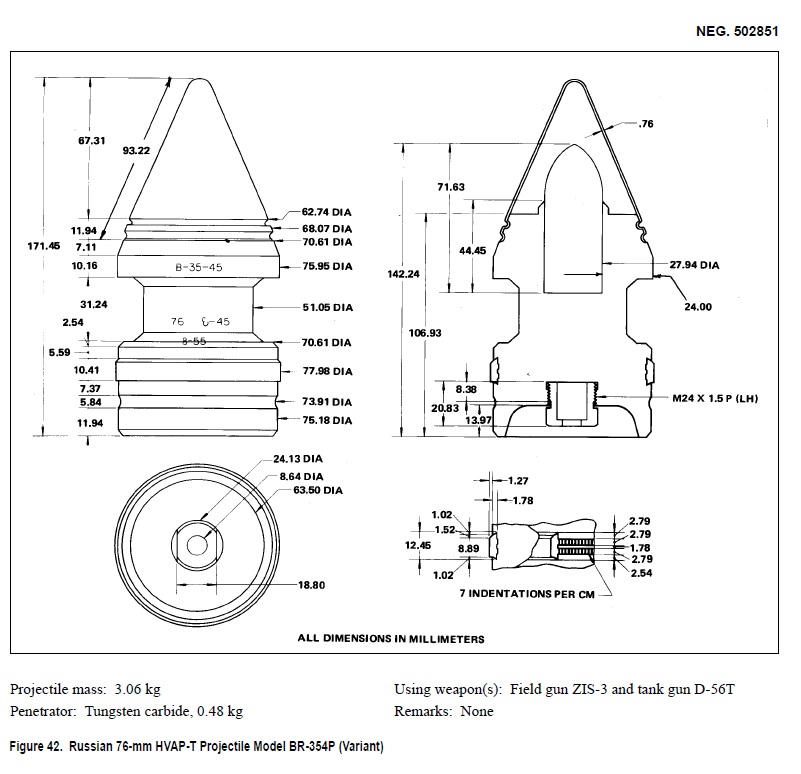
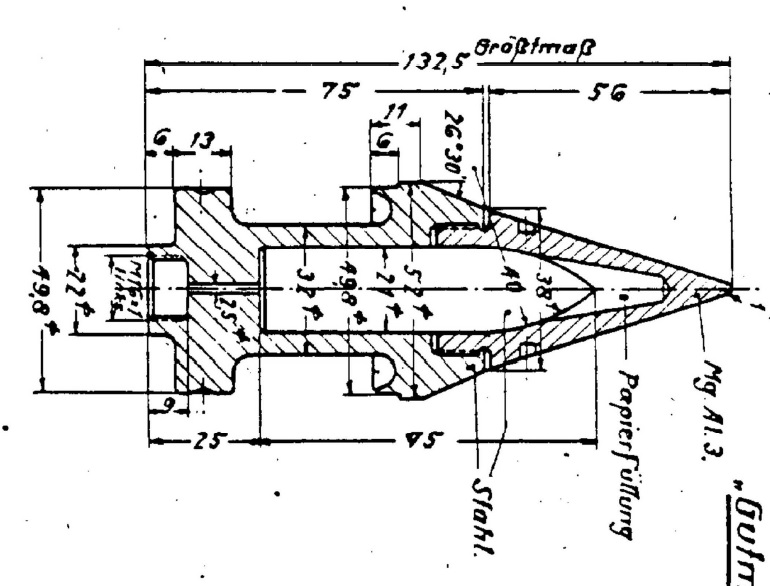
Then there is the more regular projectile-shaped APCR that is often referred to as the HVAP design.
They tend to look like these.
As you can see, there is some variation in design and material choice. But, the overall projectile shapes are very similar. For example, Soviet and German arrowhead APCR rounds, usually used steel bar stock as the carrier shell, and either an empty windscreen/ballistic cap or a paper/plastic filled one. Or in some cases, a magnesium-aluminum alloy cap to provide a flash upon impact.
The German HVAP-type rounds were usually steel bar stock carrier shells with bakelite core nose pads and aluminum or steel ballistic caps. And the US had two variants. The early variant, consisting of M304 and M93, has an aluminum body, ballistic cap, and core retention cap, with a steel base cap. And the later lightweight variant, consisting of M319, M332, and several prototypes, had an all-aluminum alloy carrier shell. Later Soviet APCR rounds copied the German HVAP design for the 85mm and 100mm guns… However, it is exceedingly difficult to find cutaway images of those two rounds.
Now on to APDS designs.
Originally, I had thought that there were only 3 APDS core generations and that that was the main factor affecting penetration ability. However, I think I have a greater understanding of what’s happening now, than I did previously. There are a few more nuances to it, as the double conical core design appears well before L28A1/L36A1/M392 in US APDS core designs.
So let us start with your early normal Ogival core-type APDS rounds. This would consist of rounds like 17pdr APDS Mk1, 20pdr Mk3, 76mm M331, 100mm 3BM8, 122mm 3BM7/11, 120mm L1, etc…
During the mid 50’s the US started designing and testing APDS projectiles using double conical nose designs, as a means to try and increase high obliquity penetration. They were doing this alongside testing of APFSDS, some of which used variants of said cores in their penetrator bodies. Projectiles based on these cores generally had similar vertical penetration to Ogival cores of the same mass and diameter.
Click here to see double conical core designs from the mid 50's
Note here, earlier in the text of the source document, it states that this projectile uses the same main penetrator body as 90/40mm T320.
Then we have the next version of APDS used by NATO countries. These all use the same base double conical Tungsten carbide core. But, they now incorporate a Tungsten alloy nose pad. This is where is where vertical penetration gets sacrificed, at the expense of increased high obliquity penetration reliability. The earliest versions of these rounds didn’t include the steel cup(tilt bearing) between the core and nose pad, the later ones did. In this case, at low obliquity, the Tungsten alloy nose absorbs some of the energy from the Tungsten carbide core, that would otherwise go into raw penetration. However, that same nose helps to increase high obliquity penetration.
This version of NATO APDS covers 105mm L28, L36/M392, DM13, etc.
Click to See this Version of APDS
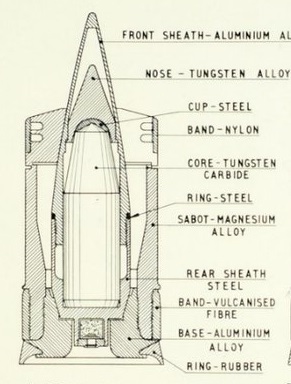
That brings us to the final version of NATO APDS. Where the transition from a Tungsten Carbide core to a Tungsten Alloy core was made. Here, a bit more vertical penetration was lost, due to Tungsten alloy being softer than Tungsten Carbide. However, the performance at high obliquity increased considerably. Also due to the difference in how the two materials perforate armor steel. One pushes its way through, and the other erodes its way through, losing mass as it does so. There are some other minor changes, like the change to a round tip, removing the need for the tilt bearing.
This version covers 105mm L52, M728, and 120mm L15.
Click to see Final version of APDS diagram
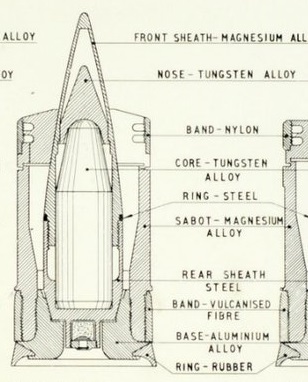
An Ansys Simulation Video that was done by SY Simulations to show the difference between Tungsten Carbide and Tungsten Alloy, especially against spaced armor plates. Velocity for both rounds is set for just under 800m.